Atlas Copco
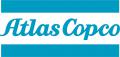
According to the first company charter from February 21, 1873, AB Atlas’s objective was to manufacture and sell all types of materials for the construction and operation of railways, as well as establish the necessary workshops. When first established, AB Atlas had an unusually high number of shareholders – 50 – none of whom held more than 10% of the share capital. The largest shareholder was the Wallenberg family, which through its bank, Stockholm’s Enskilda Bank, also provided substantial loans to the company. At the very beginning Atlas acquired one of the country’s largest railway-car makers, Ekenbergs söner in Södertälje. In 1875 production totaled MSEK 4 and the company had 780 employees. Manufacturing operations were, by Swedish standards, substantial. Atlas was the largest engineering operation in Sweden at the time.
Prior to the liquidation, Atlas management began a strategic shift towards producing more advanced products, such as steam engines and machine tools. At the turn of the century, however, about half of the company’s capacity was still devoted to producing railway cars. But during Atlas’s last years as an independent company (prior to 1917), the product mix changed. The railway equipment era was coming to an end and production of rail cars stopped in 1911. Atlas began focusing on more promising market areas and started producing well-designed machine tools and steel belt pulleys. Just before the start of World War I, Atlas entered into a new product area with great potential: compressed air machinery and compressors. Gunnar Jacobsson became a member of the Board in 1901, and in 1909 he became new managing director of Atlas. He further expanded the pneumatic range with new tools and air compressors.
To strengthen liquidity and reduce interest expenses, Atlas decided to sell off some buildings and share-holdings in 1924. A large piece of land down town Stockholm, where the workshops of Atlas had been located a half-century earlier, was sold. The most profitable parts of the Atlas operation, air compressors, pneumatic tools, and compression-ignition engines, was moved to Sickla, south-east of Stockholm. Less profitable activities such as a sheet-metal department, transportation equipment manufacturing and a carpentry workshop were shut down entirely.
After the wars, Atlas worked on increasing exports. In post-war Europe competition was tough and prices were low on drilling equipment. The general manager at the time, Walter Wehtje, realized that Atlas had to offer the customers something more than the actual drilling tool in order to compete on foreign markets. Atlas presented the “Swedish method”, a modern and lighter drilling technology, compared to conventional heavier methods. It combined a light rock drill with pusher leg and drill steels with tungsten carbide drill bits. With “the Swedish method" one man could handle one machine and the method became known all over the world as the superior productivity solution in rock drilling technology.
In 1956, this was manifested by changing the company's name to Atlas Copco. "Copco" stands for Compagnie Pneumatique Commerciale, from a Belgian subsidiary. In the same year, the Belgian compressor company Arpic Engineering NV was acquired. Production capacity at Arpic was greatly expanded during the 1960s, making it one of the world´s largest manufacturers of portable compressors. With the rapid expansion of business, Atlas Copco became more complex to manage. In 1968, a major organizational change, the divisionalization of the Group, was carried out. The Group was divided into three business areas: Mining and Construction Technique, Airpower, and Tools, all with a common sales organization.
In 1975, Atlas Copco bought a majority holding in Berema, whose lightweight, petrol-driven drills and breakers were a natural complement to Atlas Copco´s Cobra drill. In 1976 the compressor product line was complemented with small compressors through the purchase of the French company Mauguière. In the early 1980's, Airpower made several strategic purchases that substantially strengthened its business potential in the United States. The purchase of Turbonetics Inc. in 1980 gave Atlas Copco valuable knowledge about centrifugal compressors. In 1984 the purchase of Linde AG, a German company, paved the way for a similar rapid development in the field of gas compressors.
In 1987 the Chicago Pneumatic Tool Co. was acquired. Chicago Pneumatic had a very strong position in American industry and automotive workshops, and Atlas Copco became the world's largest manufacturer of compressed air tools and assembly systems. In 1990 Desoutter Brothers Plc was acquired. Desoutter has a broad base in industrial tools and assembly units and it brought about synergy in technical development, manufacturing and distribution. The electric tool manufacturers AEG Elektrowerkzeuge and Milwaukee Electric Tools were acquired in 1992 and 1995, respectively.
During 2004, the Group acquired the Drilling Solutions business in the United States, forming a new division within the Construction and Mining Technique business area. In 2005, the professional electric tools business, with the two divisions Atlas Copco Electric Tools and Milwaukee Electric Tool, was divested.